Plastic flowerpots become popular. Compared with traditional porcelain flowerpots, they require less watering and are relatively cheap in price. They are not intended to be damaged and are durable.
With the improvement of living standards, people have higher functional requirements for flower pots. Such as a pot of multi-purpose plastic flower pots, rectangular flower pots, wall-mounted flower pots, hanging pots, water storage flower pots, automatic watering flower pots, etc., are increasingly receiving people’s liking.
Flower pots are produced through injection molds, with short production cycle, large output, and long tool life. PP material is the most common, the product has thin wall thickness, light weight, and the production cycle of a planter can be as low as 6 seconds. Products can be stacked and transportation costs are cheap.
Notes on the manufacture of flower pot moulds:
1. Pay attention to the height of product stacking in the early stage.
2. Pay attention to the drafting degree to prevent the cavity from being pulled. The appearance of the product is like the stroke of the knife.
3. Pay attention to the injection pressure. If the pressure is too high, the mould life will be shortened.
4. The appearance of the flower pot can be made into a mirror surface, or it can be made into a leather pattern. It can also be the same as the provided picture. It can also add company LOGO by thermal transfer.
Tips for plastic plant flower pot moulds:
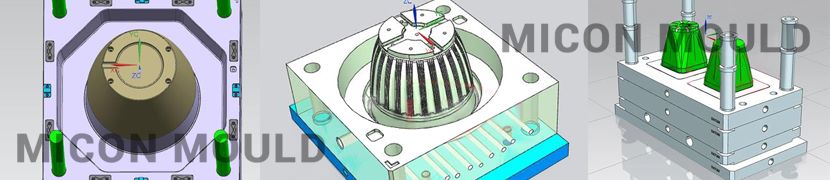
The flower pot mould has the bottom touch perforation and the side wall touch perforation to achieve water leakage (to prevent too much watering at one time to make the flowers rotten). The bottom leakage design is directly through the direct core cavity, and the punching cannot be too small, because it is too small to require high-precision machining, and the cost will increase. The sidewall leakage design uses the cylinder core to achieve the collision, which is a challenge to the complexity of the plant pot mold structure. The production cycle of the product will also be lengthened.
Flower pot mould demolding method:
The punched and perforated holes around the four sides of cavity move through the cylinder. There are two valves in the cavity to prevent the product from being stick on the cavity. The core valve + the side gas + the stripping plate are ejected to realize the automatic removal of the plant pot mould, and it can also be grasped by the robot.
The core and cavity are directly penetrated, which is economical and affordable. The plant pot mould production cycle is also short which can bring faster and greater profit margins to customers.
Micon Mould is a professional manufacturer who offers plastic injection molds for garden plant pots, flower pots, rectangular pots, round containers, square pots, thinwall garden pots, hanging flower pot mould and other gardening products. Our team consists of qualified mold makers with professional skills and solid experience in the mould making industry for more than 20 years. Tooling equipments including High Speed CNC, EDM, Wire-Cut etc. The mold steel we use is carefully selected as customer requirements.
We start with your idea and turn it into a finished working product that fully meets your expectations and specifications. Our injection mold experts look forward to working with you on your plant pot mold build project.
If you already have CAD drawings then it’s just a matter of providing a quote for the work.