Bucket in the industrial and civil are very common packages, bucket mould is our main mould series, which round bucket mould, square bucket mould, oval bucket mould, we technology has been very mature. we can making 1 cavity or 2 cavity bucket mould with 500ML, 1L, 2L, 5L, 8L, 10L, 15L, 20L, 25L.
Firstly, Mold Design and Structure
A high-quality mold structure is a premise for a qualified mold before manufacturing.We attach great importance to analyze mold structure, including demolding draft angle, the epitome of product surface, gating system design, exhaust design, cooling system design etc.The main problems that may easily occur will through trial and error during the mold structure design.
Second, the Mold Steel
In order to improve the mold life and product quality, we increase the mold steel hardness through heat treatment. The steels we commonly use are H13(48-52HRC), 2316(45-50HRC) etc.to prevent mold eccentric, we use whole piece of steel to make the bucket. The cooling system is very important. We adopt single loop cooling way and setup even distribution water channels as much as possible. To enhance the cooling effect, BeCu can be inserted on the core and cavity. Our bucket molds use air assistance, stripper plate and centre ejector for molding (release in two steps).In order to increase cooling performance, there also have water channels in the centre.
All small sliders will be nitrided to increase the hardenss.
It is important to keep maintenance for the moulds. We should check and make sure the the water channels and air circuit unlocked. Add lubricant oil for the siliders, regularly clean the stripper plate and centre ejector.
Third, the Mold Cooling system
Cooling system design is a relatively cumbersome work, namely to consider the uniformity of the cooling and the cooling effect, also the impact brings to the overall mold structure, determining the exact location and size of the cooling system; and cooling for key positions such as moving plate or the inserts, side sliders as well as side cores;standard cooling element design and the selection of the cooling standard components. Micon Mould analyzes all series of factors when begin to start the mold design. The mold has recycled water to flow in every part of it which reduces the cooling time, improves the production efficiency and greatly reduces products costs.
Whenever you need plastic paint bucket molds, please contact Micon Mould
A PROFESSIONAL CHINA PLASTIC BUCKET MOULD MANUFACTURER
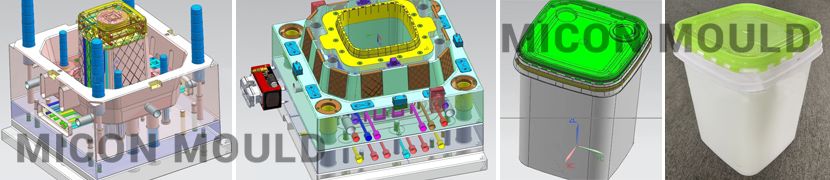
Micon Mould make bucket with shapes of round, rectangular, square and oval. Capacity from 0.5L to 25L as customers need. Use BeCu (beryllium copper) insert for better cooling, has advanced and excellent cooling system, can full automatically drop. During the past 15 years, we made so many bucket moulds for our customers, with rich experience and good price in making all kinds of bucket moulds.
Our Bucket Mould Overview:
Bucket Plastic Material: PP, PE
Bucket Mould Design: with the best optimized mold water channel arrangement design and the best cycle time performance consideration design
Steel of Cavity & Core: Up to customer’s budget and productivity required, we suggest the following steel grade:
Pre- harden steel: P20, 718
Harden steel: H13
Stainless steel : S136
Steel of Mold Base: Up to customer’s budget and requirement, we suggest different mold base steel to clients, normally use material S45C
No. of Cavity: Customized
Hardness of Cavity and Core:
Pre-Harden Steel: HRC 28~32
Heat Treatment Steel: HRC 48-52
Ejection system: Depends on the products, commonly use air, stripping plate, angel pin…etc
Cooling System:
In Core: Baffle or By pass cooling
In Cavity Plate: Chain drilling type cooling
Surface Finish: Up to the product’s requirement, normal use texture, polishing
Mold Life:
Up to mold steel grade, under ideal operation condition,
1. Pre-harden steel, 20~300000 shots
2. Harden / heat treatment steel: 60~800000 shots.
3. Stainless steel: 1 million shots.
Runner:
1. Cold runner
2. Hot runner, local brand with high quality, or appointed by customers
Delivery time: 50-55 days after mould design confirmed, presenting T1 samples
Packing: mould leg, lock block, customer demands cooling connector will be supply. Rust inhibitor will be spray before packing. Wooden box will be package outside the paint buckets mould.
Bucket mould requirements
A. Good thermostability
The mould components are complicated in shapes and it is difficult to processing after quenching. That’s why our first choice is the mould with good thermo stability. bucket mould can easily become small after heat treatment as for the expansion coefficient is relatively small, the rate of dimensional change will be reduced due to the temperature difference. If the bucket mould has a stable structure and dimension, then require no longer processing which can guarantee the mould dimensional accuracy and surface roughness requirements.
B. Sufficient surface hardness and wear resistance
Plastic bucket mould hardness is usually within 50-60HRC. The mould surface shall be sufficient in hardness after heat treatment so that the mould can have sufficient rigidity. The mould has to withstand greater compressive stress and friction as for the plastic mold filling and flow in the injection production, it requires the mould must have high shape and dimension stability, so the mould life can be ensured. However, the mould wear resistance depends on the steel chemical composition and heat treatment hardness; therefore to improve the mould hardness is conducive to improve the wear resistance.
C. Good polishing properties
The high quality bucket requires the bucket mould cavity surface roughness must be small. For example, the surface roughness of the injection mould cavity should be less Ra0.1~0.25, the optical surface should be Ra<0.1nm, the cavity shall be polished, thereby reducing the surface roughness value. Therefore the bucket mold steel should reach to these requirements: less material impurities, fine homogeneous organization, no fiber directionality, no pitting or defects in polishing.
Plastic bucket mould technical points
How to avoid the bucket mould core eccentric, which caused the bucket wall thickness not even?
1. Optimal and equal cooling effects in different area of cavity and core of the bucket moulds.
For paint bucket mould core, design the cooling channel 15mm below the molding surface.And the diameter of the paint bucket mould cooling channel should be more than 12mm, so that the water can run smoothly in the channel while taking away the heat in the core.
For paint bucket mould cavity, the cooling system design near the hot runner tip area is very important, this area is very sensitivity. Bad cooling system will directly influence the bucket’s cycle time and out looking.
Of course ,some customer want to reach high speed injection with shorter cycle time, we suggest to use BeCu insert in the core top,cavity bottom and slider.
2. The lock height of the plastic bucket moulds: In general, the lock height of the plastic bucket mould is 20%-30% than the plastic bucket. Smaller barral mould is 20% and bigger pail mould should be about 30% height.
To make a high quality painting bucket mould, we have to choose suitable steel for the bucket mould.
3. The accurate machining process to the bucket mould cavity and cores.